Stepper motors rotate a certain angle by inputting an electrical signal.
Since you can control not only the number of rotation but the rotating angle, they are used for high-precision positionings and controls.
In this section, we describe the mechanism, features, applications, and control methods of stepper motors.
Mechanism of a stepper motor
The rotor is a rotating part. It has a rotating shaft that is fitted with a cylindrical permanent magnet magnetized alternately with S and N poles.
The stator is a cylindrical part, also known as a stationary part.
The stator is a multi-pole electromagnet in which poles (iron cores) are arranged so that N and S poles appear alternately. The coil consists of two sets of phase A and phase B.
The operation principle of a stepper motor is based on electromagnetic force. A magnetic force is generated in the electromagnet of the stator by passing a current through the coil of a stepper motor, and a rotor can be rotated using the force of attraction and repulsion generated between the coil and the permanent magnet of the rotor.
A stepper motor enables accurate positioning and speed control by repeating "steps" in which the rotor rotates by a certain angle.
Specifically, the stator has multiple poles fixed so as to surround the rotor. The poles of each phase are magnetized by passing current through two sets of coils. The poles corresponding to phases A and B are positioned half relative to the magnetic pole spacing of the permanent magnet.
When the direction and strength of the current flowing through each coil is controlled by an external control circuit, each pole is excited to the S and N poles at a constant timing. The timing of this change in magnetic force causes the rotor's permanent magnets to generate rotational torque, which causes the rotor to rotate by the amount of magnetic pole spacing (steps).
One step angle of a stepper motor corresponds to the angle at which the rotor moves from the previously attracted pole to the next pole. In a word, it is determined by the number of poles. By increasing the number of poles, you can make the step angle finer.
Stepper motors are widely used in applications that require positioning and control due to their constant step angle and high accuracy.
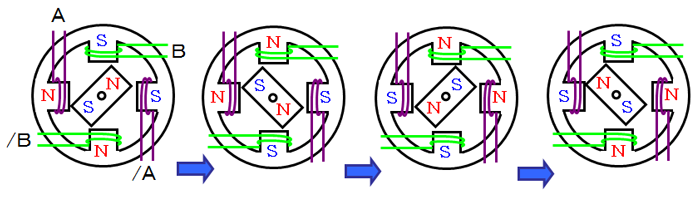
Features of stepper motors
- Positioning with high accuracy:
- Output high torque:
- Constant rotation speed:
- Maintain torque even at stop:
Stepper motor can control the rotation angle, so it enables high-precision positioning.
Stepper motors are often used in machines that need to move slowly because they can produce stable torque at low speeds.
Stepper motors rotate precisely by electrical signals, so it is easy to keep the constant rotational speed.
Since stepper motors can produce the highest torque in a stationary state, they are also used in machines that require elements such as clamps that need to hold their position in place.
Example of stepper motor use
- Printer:
- CNC machine:
- Fluid control:
- Automobile :
Used to feed paper or move the head.
Used for machine tool positioning.
Used for gas and liquid flow control.
Used for speedometer moved by a stepper motor and for adjusting the headlight position.
How to control the stepper motor
- Full-step control:
- Half-step control:
- Micro-step control:
In this method, the same level of current is applied in the two sets of coils to rotate at the same time. It provides a simple control and large torque, but cause a little high vibration.
In this method, by adding a phase that applies current to only one set of coils in the middle of the operation phase of the full step, rotation can be performed at a step angle of half the full step control. It allows smoother rotation than the full step, but the torque may be lower.
In this method, splitting the intensity of the current flowing through the coil into several stages enables even smoother rotation than half-step control. However, the positioning capability may not always be proportional to the number of segments
Items required for stepper motor controls
- Power supply:
- Motor driver:
- Microcomputer or Controller:
- Sensor (Optional):
A stepper motor requires a suitable power supply. A stepper motor may need more incoming power than a normal DC motor. It is necessary to have a suitable power supply that matches the motor size.
A stepper motor rotation is controlled by passing current with regularity, and a driver unit is required to generate this current change. The driver is responsible for receiving external signals and delivering the appropriate current to the stepper motor.
A controller is required to control a stepper motor through a driver. A microcomputer or controller can be used to send appropriate control signals to the driver.
For precise control of a stepper motor, sensors that acquire information such as position and speed are also effective. This improves the accuracy of a stepper motor.
Summary
In addition, you can choose the appropriate control method depending on your purpose such as full-step control, half-step control, or micro-step control.
When selecting a stepper motor, it is important to select an appropriate one considering the rotation angle, rotation speed, torque, control method, etc.
We offer not only stepper motors but motion control products in general.
Taking advantage of the long history of experience and expertise, we can make proposals tailored to customer specifications.
You can order from a single piece as well as applying various customization and special specifications.
If you have a trouble with motors and motion controls, please feel free to contact us. It is welcomed to give us just the idea level target you want to realize.